摩擦磨損試驗及檢測技術(shù)淺析
2014.05.10一、摩擦磨損試驗研究的必要性
要研究摩擦學(xué)的理論,確定各種因素對摩擦、磨損性能的影響,研究新的耐磨、減摩及摩阻材料和評定各種耐磨表面處理的摩擦、磨損性能,必須掌握摩擦磨損試驗技術(shù)。
摩擦磨損試驗技術(shù)包括兩個方面,即:摩擦磨損試驗方法和摩擦磨損試驗測試裝置。
二、摩擦磨損試驗的分類
目前采用的試驗方法可以歸納為下列三類:
1、實驗室試件試驗
根據(jù)給定的工況條件,在通用的摩擦磨損試驗機上對尺寸較小、結(jié)構(gòu)簡單的試件進行試驗。
由于實驗室試驗的環(huán)境條件和工況參數(shù)容易控制, 因而試驗數(shù)據(jù)的重復(fù)性較高,試驗周期短,試驗條件的變化范圍寬,可以在短時間內(nèi)取得比較系統(tǒng)的數(shù)據(jù)。
但由于試驗條件與實際工況不完全符合,因而試驗結(jié)果往往實用性較差。
實驗室試驗主要用于:各種類型的摩擦磨損機理和影響因素的研究,以及摩擦副材料、工藝和潤滑劑性能的評定。
2、模擬性臺架試驗
在實驗室試驗的基礎(chǔ)上,根據(jù)所選定的參數(shù)設(shè)計實際的零件,模擬零件的實際工作條件,進行臺架試驗。
由于臺架試驗的條件接近實際工況,增強了試驗結(jié)果的可靠性。同時,通過試驗條件的強化和嚴(yán)格控制,也可以在較短的時間內(nèi)獲得系統(tǒng)的試驗數(shù)據(jù);并且能夠預(yù)先給定可控制的工況條件,并能夠測得各種摩擦磨損的參數(shù),進行摩擦磨損性能影響因素的研究。
臺架試驗的主要目的在于:校驗實驗室試驗數(shù)據(jù)的可靠性和零件磨損性能設(shè)計的合理性。
常見的臺架試驗臺有:軸承試驗臺、齒輪試驗臺、凸輪挺桿試驗臺等。
3、實際使用試驗
在上述兩種試驗的基礎(chǔ)上,對實際零件進行使用試驗,使用試驗是在實際運轉(zhuǎn)現(xiàn)場條件下進行的。
這種試驗的真實性和可靠性最好。
但是試驗周期長、費用大,試驗結(jié)果是各種影響因素的綜合表現(xiàn),因而難以對試驗結(jié)果進行深入分析。這種方法通常用作檢驗前兩種試驗數(shù)據(jù)的一種手段。
上述幾種類型的試驗各有特點,在磨損磨損研究工作中,通常先在實驗室里進行試樣試驗,然后再進行模擬性臺架試驗和實際使用試驗,構(gòu)成一個所謂的“實驗鏈”。
三、摩擦磨損試驗的模擬問題和試驗參數(shù)選擇
1、摩擦磨損試驗?zāi)M
摩擦磨損性能是摩擦學(xué)系統(tǒng)在給定條件下的綜合性能,因此,試驗結(jié)果的普適性較低。所以在實驗室試驗時,應(yīng)當(dāng)盡可能地模擬實際工況條件。
2、試驗參數(shù)的選擇
模擬的摩擦磨損試驗系統(tǒng)中最多有四種參數(shù)可以與實際摩擦系統(tǒng)不同:①載荷;②速度;③時間;④試樣尺寸和形狀。而在其他方面,例如摩擦運動方式、引起磨損的機理、組成摩擦系統(tǒng)的各要素及其材料性質(zhì)、摩擦?xí)r的溫度及摩擦溫升、摩擦系數(shù)等模擬的和實際的系統(tǒng)兩者必須相同或相似。
四、摩擦磨損試驗機
1、摩擦磨損試驗機分類
按摩擦副的接觸形式和運動方式分:點、線、面接觸;滑動、滾動、滾滑、往復(fù)運動。

2、常用的摩擦磨損試驗機
(1)四球式試驗機
★工作原理:由四球(1個上球3個下球)組成摩擦副(如上圖所示),上球卡在夾頭內(nèi),下球組固定不動,上球與下球組相接觸。工作時,上球由主軸帶動旋轉(zhuǎn),通過加載系統(tǒng)向下球組加載。
★主要用途:主要用來評定潤滑劑的性能。
該試驗機的評定指標(biāo)有:
磨損--負(fù)荷曲線:在雙對數(shù)坐標(biāo)上,基于不同負(fù)荷下三個固定鋼球的平均磨痕直徑所作的曲線。
赫茲線:由于彈性變形所產(chǎn)生的圓形接觸面的理論直接與靜載荷的關(guān)系。
①最大無卡咬負(fù)荷PB:在試驗條件下不發(fā)生卡咬的最高負(fù)荷,它代表油膜強度。
卡咬:鋼球摩擦面之間出現(xiàn)局部的金屬轉(zhuǎn)移。這種現(xiàn)象以摩擦和磨損增大為標(biāo)志,并導(dǎo)致三個固定球上呈現(xiàn)粗糙的磨痕,轉(zhuǎn)動球上呈現(xiàn)粗糙的環(huán)。
②燒結(jié)負(fù)荷PD:試驗條件下使鋼球發(fā)生燒結(jié)的最低負(fù)荷,它代表潤滑劑的極限工作能力。
燒結(jié):試件摩擦面之間出現(xiàn)金屬熔化,并使之相互結(jié)合的現(xiàn)象,此時四個球就燒結(jié)在一起形成寶塔形。
(2)環(huán)塊式試驗機,又稱Timken(梯姆肯)試驗機。
★工作原理:主動件是標(biāo)準(zhǔn)旋轉(zhuǎn)圓環(huán),被動件是被固定的標(biāo)準(zhǔn)尺寸矩形塊。通過測量不同載荷下,被動試件矩形塊上出現(xiàn)的條形磨痕寬度,以及摩擦副材料間的摩擦力、摩擦系數(shù),來評定潤滑劑的承載能力以及摩擦副材料的摩擦磨損性能。
★主要用途:用于線接觸摩擦副的摩擦磨損試驗。
(3)銷盤式試驗機
★工作原理:試驗時,銷固定不動,盤做旋轉(zhuǎn)運動。通過力傳感器采集試驗過程總摩擦力和載荷的變化,通過位移傳感器對試樣的總磨損進行測量。
★主要用途:用于面接觸摩擦副的摩擦磨損試驗,在滑動條件下,評價材料的摩擦系數(shù)和磨損率,研究工況參數(shù)對摩擦性能和磨損機理的影響,是目前用途最廣泛的摩擦磨損試驗設(shè)備。
五、摩擦磨損試驗中的參數(shù)測量
1、摩擦系數(shù)或摩擦力的測量
①機械式:
載荷W通過上試件1加到下試件2上。下試件(半徑為r)旋轉(zhuǎn),上試件固定。試樣間的摩擦力使下主軸產(chǎn)生一個力矩,此時與主軸相連的砝碼產(chǎn)生一個偏角,來平衡摩擦力產(chǎn)生的摩擦力矩,偏角反應(yīng)了摩擦力矩P的大小,可以直接從標(biāo)尺讀出,由此摩擦力矩可以換算出試件上的摩擦系數(shù)μ
μ= P/(W r)
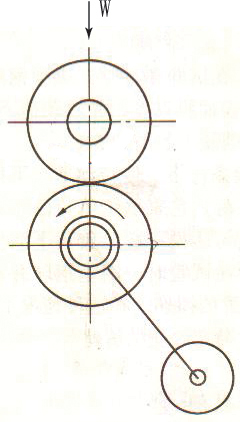
②電測法:把壓力傳感器附加到測力元件上,將摩擦力轉(zhuǎn)換成電信號,輸入到測量和記錄儀上,自動記錄下摩擦過程中摩擦力的變化。這種方法目前已普遍應(yīng)用。
2、磨損量的測量
機械零件的磨損量可以用磨下材料的質(zhì)量、體積或者磨去的厚度來表示。
① 磨損重量計量法
a.稱重法:
用稱量試件在試驗前后的質(zhì)量變化來確定磨損量。這種方法簡單,采用最普遍。通常采用精密分析天平稱重,測量精度為0.1mg。
●由于測量范圍的限制,稱量法僅適用于小試件。
●為保證稱重的精度,試件在稱重前應(yīng)當(dāng)清洗干凈并烘干,避免表面有污物或濕氣而影響重量的變化。
●對于多孔性材料,在磨損過程中容易進入油污而不易清洗,稱重法往往誤差很大。
●若試件在摩擦過程中重量損失不大,而只發(fā)生較大的塑性變形,則稱量法不能反映表面磨損的真實情況。
b.沉淀法或化學(xué)分析法:
將潤滑油中所含的磨屑經(jīng)過過濾或者沉淀分離出來,再由稱重法測量磨屑質(zhì)量。也可以采用定量分析化學(xué)的方法測量潤滑油中所含磨屑的組成和質(zhì)量。
② 磨損厚度計量法
a.測長法:
測長法是測量摩擦表面法向尺寸在試驗前后的變化來確定磨損量。
常用測量長度儀器,如千分尺、千分表、測長儀、萬能工具顯微鏡、讀數(shù)顯微鏡等。
為了便于測量,往往在摩擦表面人為地做出測量基準(zhǔn),然后以此測量基準(zhǔn)來量度摩擦表面的尺寸變化,測量基準(zhǔn)是根據(jù)試件形狀和尺寸,在不影響試驗結(jié)果的條件下設(shè)置的,其形式有:
★壓痕法:壓痕法是通過事先在試樣表面壓出壓痕,再根據(jù)磨損前后壓痕尺寸的變化來計算試樣的磨損量。
如磨損試驗前用維氏硬度計壓頭在試樣表面上打出壓坑,如圖所示,測出其對角線長度d2,試驗后再測出壓痕的對角線長度d1,則試驗中磨損的深度為:△h=(d2-d1)/m。
因為壓痕過程并非是完全塑性變形, 所以壓坑與壓頭的形狀不完全相同。
考慮彈性變形的影響應(yīng)將m 數(shù)值增大。當(dāng)錐面角α=136°時, 根據(jù)經(jīng)驗可按以下數(shù)值選取:塑性良好的金屬例如鉛, 選取m=7; 鑄鐵, 選取m=7.6 ~ 8.2;軸承鋼, 選取m=7.7~8.4。
壓痕法產(chǎn)生誤差的另一個因素是壓坑四周形成鼓起, 使表面形狀變化,并影響摩擦副的配合性質(zhì)和磨損測量精度。
★切槽法:切槽法測磨損與壓痕法十分相似, 用回轉(zhuǎn)刀具刻出月牙形槽,切槽法排除了彈性變形回復(fù)和四周鼓起的影響。根據(jù)幾何關(guān)系,切槽寬度和磨損深度的關(guān)系為:
r-刀刃的回轉(zhuǎn)半徑;R-試件的表面曲率半徑,平面時R=∞,凸面用“+”,凹面用“-”
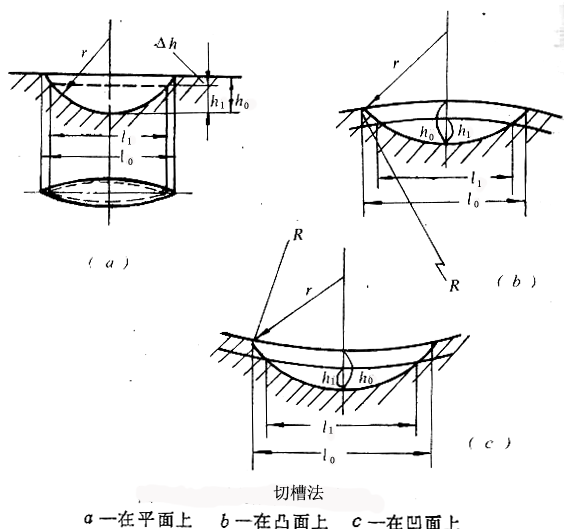
b.表面輪廓法:
當(dāng)磨損厚度不超過表面粗糙峰高度的磨損時,用表面輪廓儀可以直接測量磨損前后表面輪廓的變化來確定零磨損量。
當(dāng)測量磨損厚度超過表面粗糙度的磨損必須采用測量基準(zhǔn)。下圖給出兩種測量基準(zhǔn), 圖(a) 是用未磨損表面作為基準(zhǔn), 而圖(b)是在表面上開設(shè)一個楔形槽, 根據(jù)磨損前后楔形槽寬B和b的數(shù)值計算磨損厚度h。
c.非接觸式測量法:
以上測量磨損量的方法都要拆卸部分機器零件,當(dāng)重復(fù)試驗時,反復(fù)拆卸會改變試樣的相對位置,破壞摩擦表面的磨合性。用非接觸式測量法可以避免這方面的缺陷。
非接觸式測量磨損方法的原理如圖所示:非接觸式傳感器裝在靠近基準(zhǔn)板的地方。此基準(zhǔn)板與上試樣連為一體。
當(dāng)磨損使上試件下沉?xí)r,則傳感器與基準(zhǔn)板之間間隙增加,傳感器得到此位移信號,經(jīng)儀表檢測放大就可以反映出磨損變化情況。
③ 磨損體積計量法
a.放射性同位素法:
將摩擦表面經(jīng)放射性同位素活化, 則在磨損過程中落入潤滑油中的磨屑具有放射性。因此定期地測定潤滑油的放射性強度, 就可以換算出磨損量隨時間的變化。
放射性同位素方法最大的優(yōu)點是測量磨損量的靈敏度高, 可達10-7~10-8g。
沉淀法(或化學(xué)分析法)和放射性同位素法這兩種方法測量的是整個表面的總磨損量,無法確定摩擦表面的磨損分布。此外,潤滑油的合理取樣是保證測量精度的關(guān)鍵。
3、摩擦溫度的測量
摩擦?xí)r,接觸表面溫度高低和分布情況對摩擦磨損性能影響很大,因此測量摩擦表面溫度很重要。
測量摩擦副表面溫度的主要方法有熱電偶和遠紅外輻射測溫法。
六、磨損微粒的分析技術(shù)
對磨損產(chǎn)物-磨粒的成分和形態(tài)的分析,不僅是研究磨損機理的主要方法之一,而且是工程上磨損預(yù)測和工程監(jiān)控的重要手段。
1、光譜分析法:
光譜分析是利用組成物質(zhì)的原子在一定條件下能發(fā)射具有各自特征的光譜的性質(zhì),用來分析潤滑油中的金屬含量。
因為每種元素都有各自的特征光譜線,并且每種元素所發(fā)射特征光譜線的強度都與它在物質(zhì)中的含量有關(guān),所以可通過對光譜分析,確定物質(zhì)中含有的化學(xué)成分及含量。
光譜分析法具有極高的靈敏度和準(zhǔn)確度,且分析速度快,通常應(yīng)用于鐵路機車和船舶柴油機以及航空發(fā)動機的磨損檢測,以防止故障發(fā)生。
2、鐵譜分析法:
分析式鐵譜儀的結(jié)構(gòu)原理如圖所示:從運轉(zhuǎn)的摩擦機械系統(tǒng)的潤滑劑中提取一定量的油樣,經(jīng)過能促進磨損微粒沉淀的特殊溶劑稀釋后,由低流量泵送到并流過透明基片。由于基片是裝在略微傾斜的斜面上的,磁場力呈梯度分布,所以微粒就粘附在底片上并接近按大小分布。基片上的磨粒經(jīng)去油和固定后,便制成了鐵譜圖。
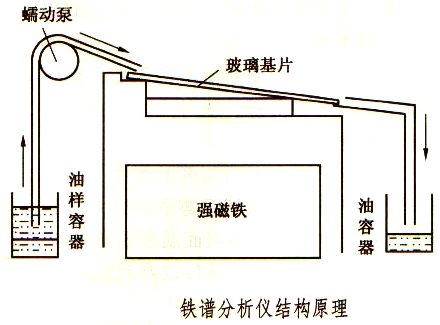

①定性鐵譜分析:利用光學(xué)顯微鏡對鐵譜片上沉淀的磨粒進行形貌、尺寸大小和成分的分析,建立磨損狀態(tài)類型與磨損顆粒形態(tài)的相互關(guān)系,判別摩擦副的磨損程度以確定失效情況和磨損部位。
例如:正常磨損的磨屑一般呈薄片狀;
磨粒和切削磨損形成的磨屑具有螺旋狀或卷曲狀,這種磨粒的集中出現(xiàn)是嚴(yán)重磨損過程的表現(xiàn),若數(shù)目急劇增多,則表面機器損壞即將開始。
氧化磨損或腐蝕磨損形成的磨屑是由化合物組成的,在有色光作用下不同成分的磨料顯示出不同的顏色,以此確定磨粒的材料類型,進而判斷磨損的具體位置。
②定量鐵譜分析:
通常先采用鐵譜光密度計來測量鐵譜片上不同位置上磨粒沉積物的光密度,從而求得磨粒的尺寸、大小分布以及微??偭?。
所謂光密度是投射過透明鐵譜片的光強度與透射過含有磨粒的鐵譜片的光強度之比,與磨屑的覆蓋面積成正比,那么用光密度值就可以推算鐵譜片上磨屑量的多少。
一般在鐵譜片上55mm(大磨粒沉積處)和49mm(小磨粒沉積處)兩處測量磨粒的光密度,以AL和AS分別表示大、小磨粒光密度的讀數(shù)。通過測出鐵譜片上大、小磨粒的光密度,由此確定大磨粒和小磨粒的相對含量。
當(dāng)機器在正常運轉(zhuǎn)狀態(tài)下(除磨合階段外), AL一般稍大于AS,但差別不顯著,這說明磨損處于穩(wěn)定狀態(tài)。在非正常磨損狀態(tài)下, AL將顯著地大于AS,而且磨粒量急劇增多。
因此,磨損變化程度可用磨粒數(shù)量和大小磨粒數(shù)量差值兩個特征量表示。
總磨損量Iq= AL + AS ,表示不同時間磨粒數(shù)量的變化,對應(yīng)于機器的磨損量和磨損率,當(dāng)嚴(yán)重磨損開始時,其數(shù)值急劇增大,稱為磨損定量指數(shù)。
大小磨粒數(shù)量差值Is= AL-AS表示不同時間磨粒尺寸比例的相對變化,反映磨損不正常程度,其數(shù)值越大說明磨損越惡化, 故稱為磨損嚴(yán)重性指數(shù)。
綜上兩個方面的影響因素,對于整個磨損情況可以用磨損指數(shù)方程:

在磨粒分析方面,鐵譜和光譜分析各有所長。
★鐵譜法能將磨粒按尺寸大小排列,并反映出顆粒的形狀、磨損的性質(zhì),但進一步定性定量分析有困難;
★光譜法能夠區(qū)別磨粒的中含有的元素成分及含量,但對于大于2μm的微粒即失去檢測的效能,而很多機械失效時,磨粒尺寸往往大于2 μm 。因此,分析磨粒最好兩種方法聯(lián)合使用,可以相互補充,使檢測效果較好。
七、摩擦表面的形態(tài)分析
由于摩擦現(xiàn)象發(fā)生在表面層,表層組織結(jié)構(gòu)的變化是研究摩擦磨損規(guī)律和機理的關(guān)鍵,現(xiàn)代表面測試技術(shù)已先后用來研究摩擦表面的各種現(xiàn)象。
1、摩擦磨損表面形貌的分析
摩擦過程中表面形貌的變化可以采用表面輪廓儀和電子顯微鏡來進行分析。
表面輪廓儀是通過測量觸針在表面上勻速移動,將觸針隨表面輪廓的垂直運動檢測、放大,并且描繪出表面的輪廓曲線。再經(jīng)過微處理機的運算還可以直接測出表面形貌參數(shù)的變化。
目前常用的表面微觀形貌分析設(shè)備為掃描電子顯微鏡。電子掃描的圖像清晰度好,并有立體感,放大倍數(shù)變化范圍寬(20-20000倍),檢測范圍亦較大。
2、摩擦磨損表面結(jié)構(gòu)的分析
金屬表面在摩擦磨損過程中表層結(jié)構(gòu)的變化通常用衍射技術(shù)來分析,常用的有電子衍射法、 X射線衍射法 。
★電子衍射的穿透能力小,散射厚度僅為10-7~10-8cm。電子衍射儀可用來進行薄層的摩擦表面分析, 例如研究金屬的粘著磨損和摩擦副材料遷移現(xiàn)象。
★X射線穿透能力大,散射層厚度可達到10-4~10-2cm。X 射線衍射儀常用來對較厚的摩擦表面的結(jié)構(gòu)分析。例如,此法常用于研究發(fā)動機活塞環(huán)與缸套表面摩擦磨損后晶體尺寸的變化,單晶鐵板在磨料磨損后由α鐵向γ鐵的轉(zhuǎn)變以及潤滑油添加劑在金屬表面上的潤滑機理。
3、摩擦磨損表面化學(xué)成分的分析
摩擦表化學(xué)元素的組成與分布特點可用能譜分析和X射線顯微分析方法來進行。
★能譜分析的基本原理:是用X射線、真空紫外光束或電子束照射試件表面使表面受到激發(fā)而產(chǎn)生光電子和俄歇電子,然后測量和分析這些電子的能量,就可確定表面的化學(xué)成分。
★X射線顯微分析的基本原理:是通過電子束對試件表面作用,使各元素發(fā)出相應(yīng)特征的射線譜,以不同特征X射線的波長和強度來確定元素的成分和含量。